AIR CLASSIFYING MILL/ACM
Air Classifying Mill operates on the principle of impact grinding and employs high rotor speeds with a striking edge velocity of up to 120 m/s. Size reduction takes place by the impact of material particles on the rotating grinding surfaces (hammers or pins) and on the fixed liner or grinding track. Air Classifier Mills are designed for producing micro-fine particle size. High air, unique multi teeth rotor and serrated liners fitted in the air classifier mills create numerous air whirls, turbulence and progressive grinding.
The air classifier mills are designed to control the top cut size, great turbulence, and high air whirls to ensure minimum temperature increase to handle heat sensitive materials. The classifier retains coarser particles while suction fan discharges fine powder through cyclone separators and dust is collected in filter bag units. All air classifier mills are supplied with pneumatic conveying system.
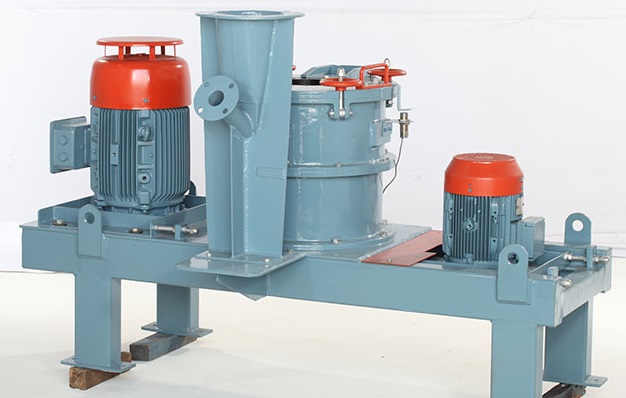
The working principle of an air classifying mill involves the following steps:
Material Introduction: The material to be processed is introduced into the mill chamber through a feed inlet. It can be in the form of dry powder or a mixture of particles and air.
Grinding: The material is subjected to grinding or pulverization as it comes into contact with the rotating grinding elements inside the mill. These elements can be hammers, pins, or blades, depending on the specific design of the mill.
Air Classification: As the ground material is transported by the airflow generated by the rotating blades, the particles are subjected to centrifugal and drag forces. These forces cause the particles to separate based on their size and density.
Particle Separation: The airflow carries the finer particles upward, while the larger particles, which have higher inertia, tend to move towards the periphery of the mill chamber and eventually fall due to gravity. The separated particles are collected in different chambers or outlets, allowing for the desired particle size distribution.
Recirculation: In some air classifying mills, a portion of the coarse particles may be recirculated back into the grinding chamber for further grinding, while the fine particles are collected as the final product.
Air classifying mills offer several advantages, including:
Particle size control: They provide precise control over the final particle size distribution, allowing for the production of uniform and consistent products.
Efficient grinding: The combination of grinding and classification in a single unit improves the overall efficiency of the milling process.
Versatility: Air classifying mills can handle a wide range of materials, from soft to hard, brittle to fibrous, and even heat-sensitive materials.
Dust control: The use of an air classifier helps in controlling the release of dust and fine particles into the surrounding environment.
KEY BENIFITS
- Modern, Economical, simple
- High Pressure Mills for dust explosive materials
- Closed Loop systems in inert atmosphere for explosive, heat sensitive and hygroscopic materials.
- Heat Exchanger based cool grinding system for non-explosive heat sensitive material.
- Grinding and Classifying in one machine with online granulation adjustment
- Dust free Operation
- Uniform particle size distribution with narrow bandwidth.